Tips for air compressor energy saving in winter (I)
The operating characteristics and environmental changes of air compressors in winter require us to take a series of effective energy-saving measures to ensure the efficient operation of the equipment. The following are 10 tips for winter energy saving to help you optimize the operation of air compressors and reduce energy consumption.
1. Choose the right lubricant viscosity grade
It is recommended to use synthetic lubricants with lower viscosity in winter. These lubricants have good fluidity at low temperatures, which can reduce internal friction of air compressors, reduce energy consumption, and extend the service life of equipment.
2. Check and replace air filters regularly
The air is dry in winter, and dust and impurities can easily clog air filters. Check the air filter regularly and clean or replace the clogged filter element in time to reduce intake resistance and improve efficiency.
3. Optimize air compressor operating parameters
According to the actual gas demand, set the working pressure reasonably to avoid unnecessary energy consumption caused by excessive pressure. For every 1 bar increase in pressure, energy consumption will increase by about 7%. Ensure that the air compressor operates at a reasonable pressure to avoid energy loss caused by frequent start and stop.
4. Use frequency conversion control technology
The frequency conversion air compressor can automatically adjust the motor speed according to the actual gas consumption, effectively reducing energy consumption. The frequency conversion technology has a small starting current and a small impact on the power grid, which can extend the service life of the air compressor.
5. Regularly check and maintain the condensate discharge system
If the condensate is not discharged in time, it will affect the quality of the compressed air and may cause equipment failure. Regularly check the drainage system, install automatic drainage devices, reduce manual operation errors, and ensure that the condensate is discharged in time.
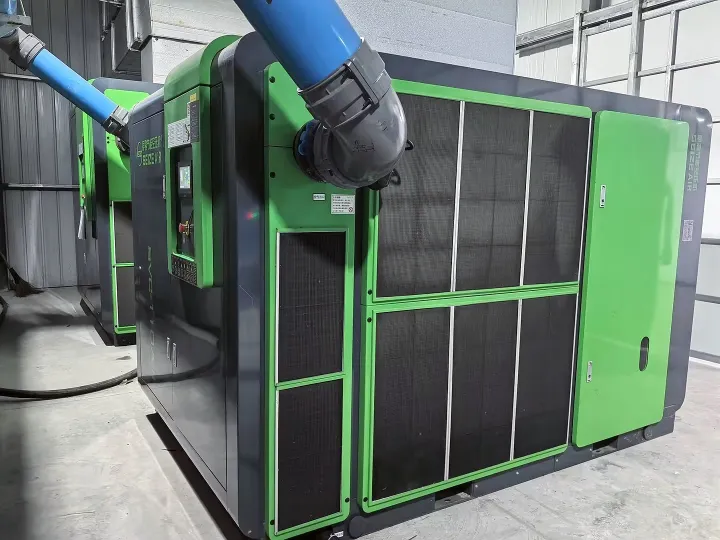
6. Reasonable use of air compressor waste heat
The air compressor will generate a lot of heat energy during operation, which can be used for workshop heating, preheating boiler water, etc. through the heat recovery system to save energy and improve system efficiency.
7. Regularly check and maintain the motor and transmission system
The efficiency of the motor and transmission system directly affects the energy consumption of the air compressor. Regularly check the motor bearings and transmission belts, replace worn parts in time, and lubricate and maintain the motor to reduce energy waste.
8. Reasonable selection of air compressor capacity
The capacity of the air compressor should be selected according to the actual gas demand to avoid excessive or too small air compressors that increase energy consumption. For gas demand with large fluctuations, multiple air compressors can be selected to run in parallel for flexible adjustment.
9. Regularly check and maintain the pipeline system
Leakage and blockage of the pipeline system will increase energy consumption. Regularly check whether there are leaks in the pipeline, repair it in time, clean the inner wall of the pipeline, and avoid pressure loss and energy waste caused by pipeline problems.
10. Use a centralized control management system
Through the centralized control system, multiple air compressors can be managed intelligently, and the equipment operation status can be automatically adjusted according to the changes in gas consumption, thereby improving the overall efficiency of the system.