Pre-Startup Inspection and Preparation for Air Compressors After Long-Term Shutdown
Air compressors are essential equipment in industrial production, and before restarting after a long-term shutdown, a thorough inspection is necessary to ensure safe and stable operation, avoiding potential failures and damage.
1. Visual Inspection
Clean the Surface of the Equipment
After a long shutdown, dust, oil, and other debris may accumulate on the equipment surface. The first step is to clean the surface, ensuring the radiators and vents are clear to prevent poor heat dissipation.
Check Fasteners
Inspect bolts and fasteners for looseness, particularly at the base and pipe connections. Make sure everything is tightly secured to prevent any loosening during operation.
Examine Cables and Wiring
Check if the power cables and control wiring are aging or damaged, and ensure all connections are secure to maintain electrical safety and reliability.
2. Lubrication System Inspection
Check Oil Level
The lubricant level may drop after a long period of shutdown. Ensure that the oil level is within the normal range and add more if necessary.
Change the Lubricating Oil
Lubricating oil may deteriorate after being idle for an extended period. It is recommended to replace the lubricating oil entirely and clean the oil circuit to ensure proper lubrication.
Check the Oil Filter
The oil filter may become clogged with impurities over time. Inspect and clean the filter, and replace it if necessary.
3. Cooling System Inspection
Inspect the Cooler
After downtime, the cooler may accumulate dust or scale, affecting its cooling performance. Clean the cooler surface to maintain proper heat dissipation.
Examine the Cooling Fan
Check if the fan blades are intact and if the motor operates smoothly. If there is any unusual noise or obstruction, perform maintenance or replace the fan.
Check the Cooling Water System
For water-cooled compressors, inspect the water pipes for blockages, ensure the water pump is working properly, and verify that the water quality is suitable for cooling.
4. Air Circuit System Inspection
Check the Air Intake Filter
After a long shutdown, the intake filter may be clogged with dust. Clean or replace the filter to maintain proper intake efficiency.
Inspect Pipes and Valves
Check the intake and exhaust pipes and valves for air leaks or blockages, ensuring the air circuit is unobstructed.
Inspect the Air Receiver Tank
Check the air receiver tank for accumulated water or rust. Clean the tank as needed to ensure safe air storage.
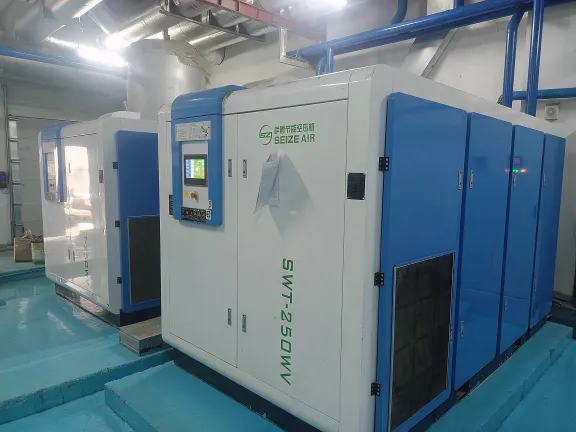
5. Electrical System Inspection
Check Motor Insulation
Use a megohmmeter to check the motor insulation performance to ensure it meets safety standards. If the insulation resistance is too low, dry the motor or replace it.
Inspect the Control Panel
Check the buttons, touchscreen, indicators, and other components on the control panel to ensure the control system functions properly.
Check the Power Supply Voltage
Ensure that the power supply voltage is stable and matches the compressor’s rated voltage to avoid equipment damage due to unstable voltage.
6. Preparation Before Trial Run
Manual Crank Over
Before starting the compressor, manually rotate the parts to check if the motor and main unit turn smoothly. This helps detect any stiffness or unusual noise.
Momentary Test Run
After ensuring that all checks are complete, perform a momentary test run to observe the compressor’s operation. This allows you to ensure everything is functioning properly.
Gradual Load Application
After starting, gradually apply the load rather than running at full capacity immediately. This ensures that the parts of the equipment adapt gradually, minimizing mechanical shock.
7. Precautions
Follow Operating Procedures
When checking and starting the air compressor, follow the equipment manual and operating rules to prevent damage caused by improper handling.
Regular Maintenance
Even if the air compressor is idle for a long time, it is essential to perform regular checks and maintenance to keep the equipment in good condition.
Record Inspection Results
It is recommended to document the results of each inspection and maintenance task, making it easier to track the equipment’s condition and address any issues that arise.
Conclusion
Air compressors that have been idle for a long period require a thorough inspection and preparation before restarting. Through visual inspections, lubrication system checks, cooling system checks, air circuit system inspections, and electrical system evaluations, the compressor can be safely and reliably restarted. Regular checks and maintenance will prolong the lifespan of the compressor, ensuring its long-term, efficient operation.