Discover the top 10 benefits of oil-injected screw compressors in industrial settings, including energy efficiency, operational cost savings, and extreme environment adaptability. Access industry-proven data and selection guidelines.
Industry Overview
As a cornerstone of modern industrial power systems, oil-injected screw compressors play a vital role in automotive manufacturing, food processing, mining, and more. Their oil-cooling mechanism outperforms oil-free models in energy efficiency and durability. This article breaks down the ten competitive advantages of this technology.
Core Benefits Breakdown
1. Dual-Engine Energy Efficiency
Variable Speed Drive (VSD) Integration
Modern compressors equipped with VSD adjust motor speed to match air demand, reducing energy costs by up to 35% for cyclical operations.
Thermal Management Innovation
Oil circulation minimizes heat generation, cutting energy waste by 15–20% compared to oil-free models. A 2023 retrofit at a Volkswagen plant in Germany reported annual electricity savings exceeding $120,000.
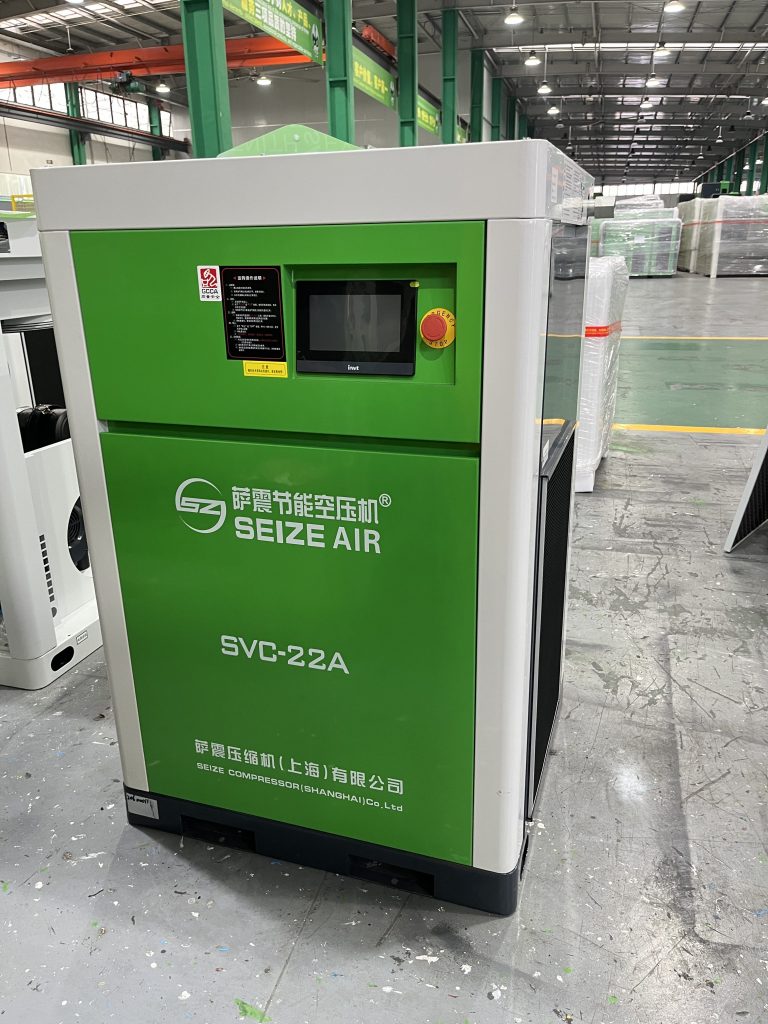
2. Lifecycle Cost Optimization
Lower Initial Investment
Upfront costs are 20–30% cheaper than oil-free alternatives, ideal for SMEs upgrading equipment.
Maintenance Efficiency
- Monthly checks: Oil levels/filter status
- Annual inspections: Rotor alignment
Simplified protocols reduce unplanned downtime by 40%. An Indian textile factory boosted productivity by 30% post-upgrade.
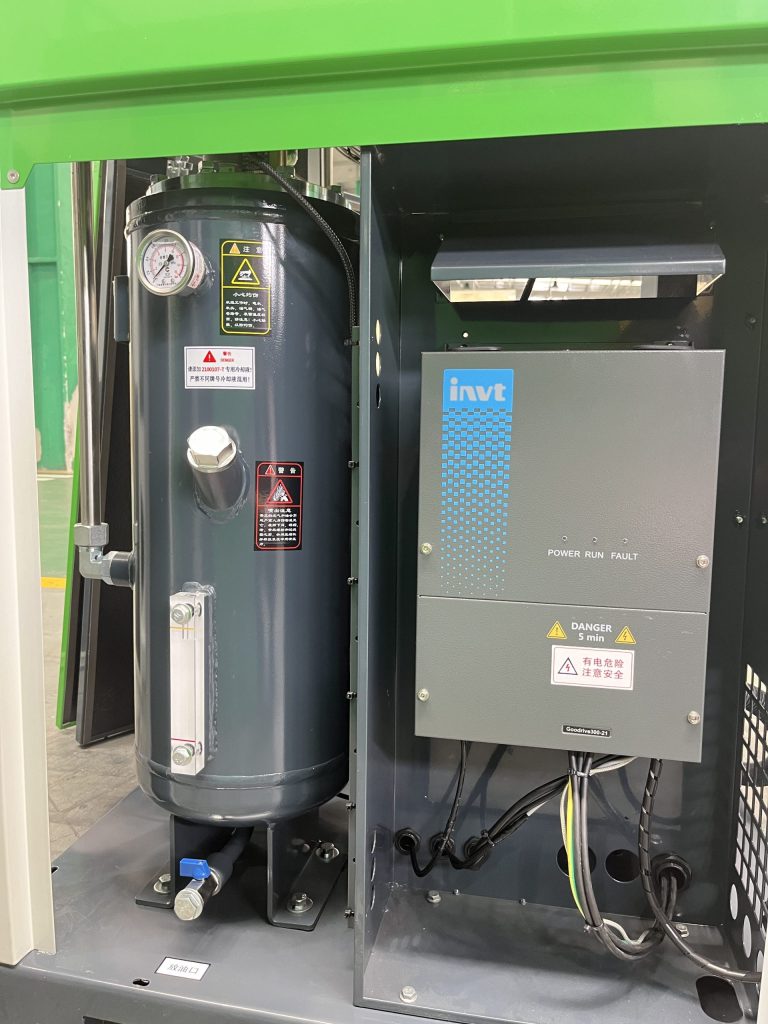
3. Extreme Environment Resilience
Operational Thresholds
- Temperature range: -10°C to 45°C
- Humidity tolerance: 95% RH
- Stable performance in dusty conditions
An Australian mining company achieved 18 months of zero breakdowns in harsh extraction sites.
4. Premium Air Output Quality
ISO 8573 Compliance
With triple filtration, these compressors deliver Class 0 air purity (<0.01 mg/m³ oil residue), meeting pharmaceutical-grade standards.
Pressure Stability
Twin-screw design ensures <1% pulsation, critical for CNC machining and precision painting.
5. Sustainable Operations
Carbon Reduction Impact
A 100 kW unit reduces CO₂ emissions by 45 tons annually, aligning with EU 2030 carbon neutrality goals.
Oil Recycling Programs
Leading manufacturers offer lubricant recovery services, achieving over 92% reuse rates.
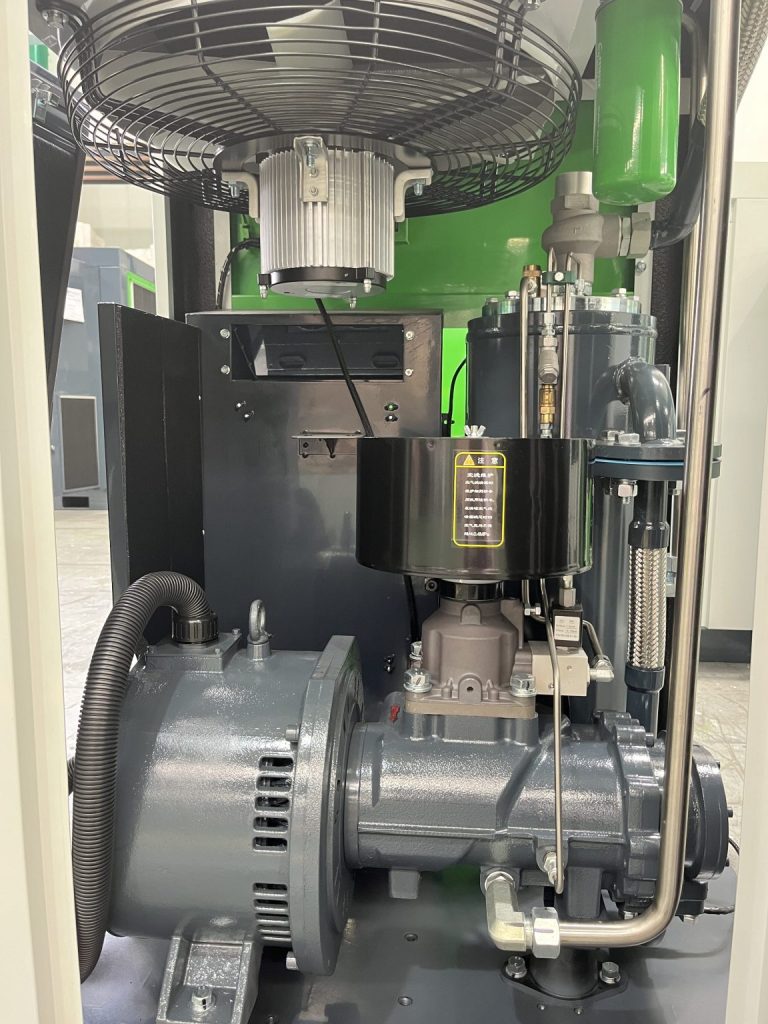
Technology Advancements
Industry 4.0 Integration
- IoT real-time monitoring (bearing vibration/temperature alerts)
- Cloud-based energy analytics
- Hybrid renewable energy compatibility
Selection Guide
- Calculate air demand (CFM/PSI)
- Evaluate site conditions
- Opt for NSF-certified food-grade lubricants (H1/H2 standards)
Request Customized Solutions
[Insert Company Website Link]
Expert support includes:
✅ On-site air audit
✅ Lifecycle cost simulation
✅ Trade-in program consultat
Website:https://seizeair-in.com
WhatsApp:WhatsApp:https://wa.me/8615121141521
发表回复