Oil-Gas Separation in Oil-Injected Screw Air Compressors
Oil-injected screw air compressors are essential in many industries, and one of the critical components is the oil-gas separator, which separates oil from the compressed air. The separation process involves several stages and principles, ensuring cleaner air and efficient operation.
1. Formation of Oil-Gas Mixture
In these compressors, lubricating oil is injected into the compression rotors. The oil mixes with the compressed air, forming an oil-gas mixture that needs to be separated before the air is delivered.
2. Oil-Gas Separation Process
Coarse Separation:
When the oil-gas mixture enters the separator, larger oil droplets are removed through gravitational settling and centrifugal force. Baffles inside the separator help capture these large droplets, which then fall to the bottom.
Fine Separation:
The remaining fine droplets are filtered out by a coalescing filter or similar media. Smaller oil droplets combine into larger ones, which are separated by gravity, leaving clean, oil-free compressed air.
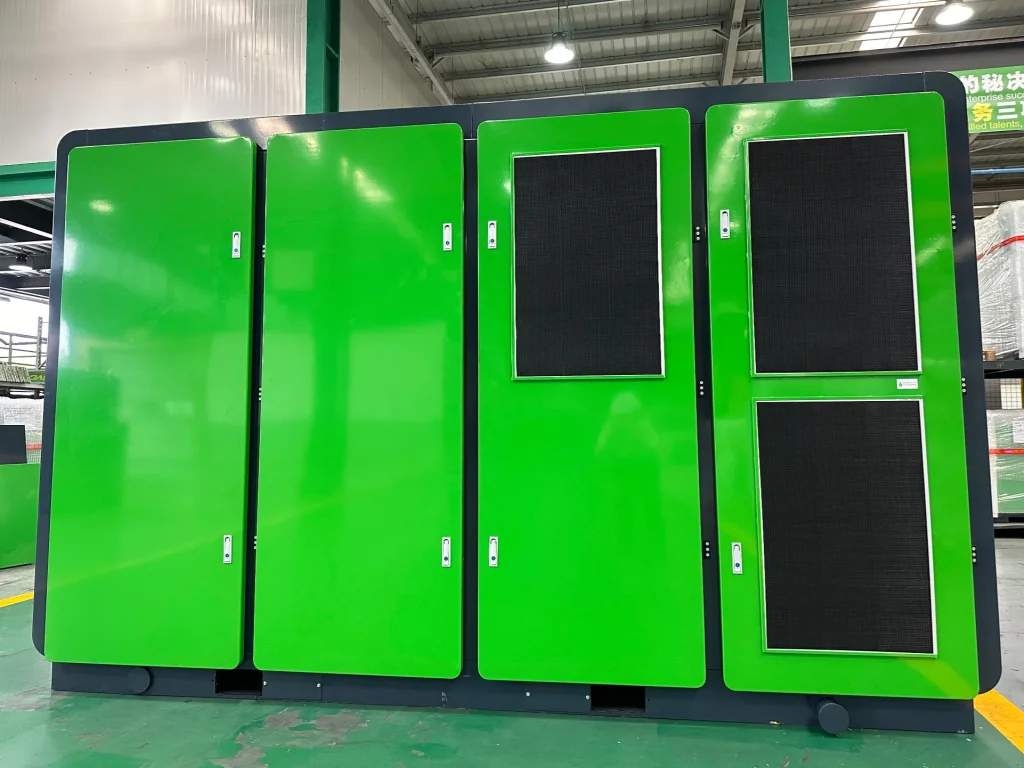
3. Key Factors Affecting Separation Efficiency
Droplet Size: Larger droplets are easier to separate.
Gas Flow Rate: Slower flow improves separation efficiency.
Separator Design: The design of the separator, including internal filters and baffles, enhances oil removal.
4. Importance of Oil-Gas Separators
A well-functioning oil-gas separator is crucial for maintaining compressed air purity and ensuring that air leaving the compressor is free of oil. This also helps reduce maintenance costs and improves the longevity of the compressor by preventing oil contamination in downstream equipment.
The oil-gas separation process in screw compressors combines centrifugal force, gravity, and filtration to efficiently separate oil from compressed air. With the right separator design and optimized conditions, compressors can operate more efficiently and last longer, providing clean air for industrial applications.