Importance of insulation for air compressors and post-processing equipment: key to ensuring efficient and stable operation
Air compressors and post-processing equipment play a vital role in industrial production. In low temperature environments, equipment may face problems such as increased viscosity of lubricating oil and freezing of condensed water, leading to failures, reduced efficiency and production stagnation. Therefore, insulation measures are essential to ensure stable operation of equipment and improve production efficiency.
1. Ensure normal operation of equipment
Prevent increase in lubricating oil viscosity
Low temperature will cause increased viscosity of lubricating oil, affecting the start-up and operation of air compressors. Insulation measures can maintain equipment temperature, prevent lubricating oil from thickening, ensure smooth start-up of air compressors and reduce wear, and extend equipment life.
Prevent condensed water from freezing
Air compressors produce moisture during the air compression process, which may freeze at low temperatures, causing pipes and valves to be blocked. Insulation measures help maintain temperature stability, prevent freezing, and ensure normal operation of equipment.
Maintain optimal operating temperature
At low temperatures, equipment performance decreases and energy consumption increases. Insulation can keep equipment working at optimal temperatures, improve efficiency, reduce energy consumption, and thus optimize the performance of compressed air systems.
2. Improve the quality of compressed air
Prevent water vapor condensation
When the temperature difference is large, water vapor is easy to condense in the pipe, affecting the air quality. Effective insulation can prevent condensation, ensure the normal operation of post-processing equipment (such as cold dryers and adsorption dryers), and ensure air quality.
Prevent pipe condensation
Uninsulated pipes are prone to condensation, which affects air quality and may cause corrosion. Insulation helps to keep the pipe temperature stable, reduce condensation, and ensure system reliability.
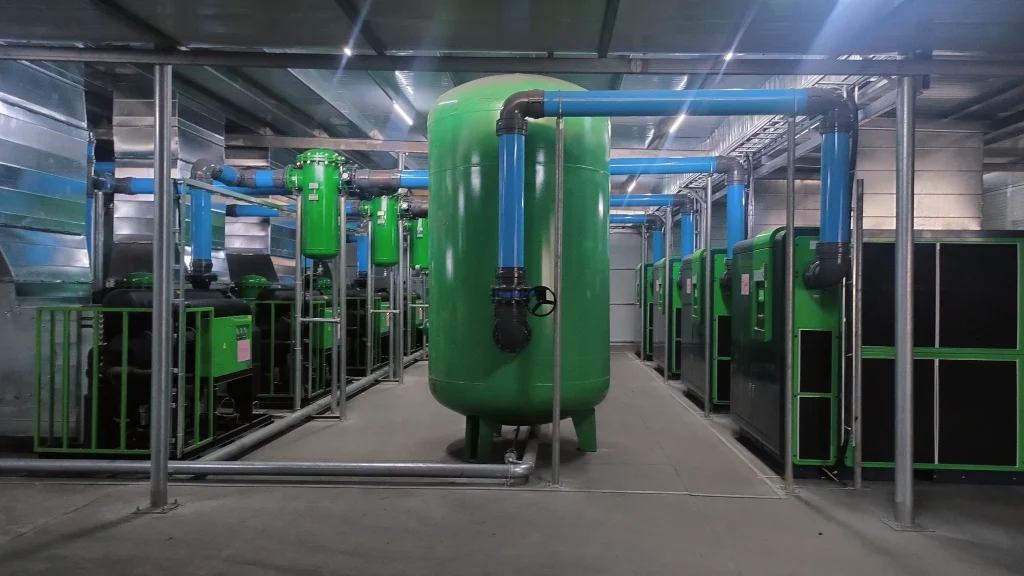
3. Energy saving and consumption reduction, reduce costs
Reduce air compressor power consumption
Air compressors are the main source of energy consumption in compressed air systems, and low temperature environments will increase power consumption. Insulation measures can reduce heat dissipation and keep equipment running at a suitable temperature, thereby reducing energy consumption and saving energy costs.
Improve the efficiency of post-processing equipment
Post-processing equipment such as cold dryers are overloaded in low temperature environments. Insulation can reduce their burden, improve efficiency, and further reduce operating costs.
4. Improve production efficiency
Reduce equipment failure downtime
Low temperature may cause equipment failure and lead to production stagnation. Insulation measures reduce failures, ensure stable operation of equipment, and improve the continuity of production lines.
Stable air supply quality
The compressed air provided by the air compressor is crucial in many industrial applications. Insulation helps maintain temperature stability and avoid temperature fluctuations that affect air quality, thereby improving production efficiency and product quality.
Insulation of air compressors and post-processing equipment is essential for equipment operation, air quality, energy efficiency, and production efficiency. Through reasonable insulation measures, not only can the equipment be guaranteed to operate stably in cold environments, reduce failures and energy consumption, but also improve air quality and production efficiency, and reduce operating costs. Therefore, implementing an effective insulation solution is an important means to improve equipment performance, extend service life, and reduce costs, which can help companies improve their market competitiveness.