Comprehensive Guide to Air Compressor Management: Improving Efficiency and Energy Saving
In modern industrial production, managing air compressors effectively is key to enhancing operational efficiency and energy savings. Proper management not only boosts machine performance and reduces downtime but also delivers significant cost savings in energy consumption.
1. Daily Maintenance: Ensuring Long-term Reliable Operation
Routine maintenance is the foundation of air compressor management, directly impacting equipment performance and lifespan. Regular checks and upkeep help prevent failures and ensure smooth operation:
Lubrication Management: Regularly check and replace lubrication oil to reduce wear and overheating, ensuring smoother operation and longer lifespan.
Filter Replacement: Clean or replace air and oil filters to keep contaminants out and improve efficiency.
Cooling System Checks: Regularly inspect the cooling system to prevent overheating, which could damage the machine.
2. Real-time Monitoring: Optimizing Efficiency and Early Issue Detection
Advanced monitoring systems allow real-time tracking of the compressor’s condition. Key parameters include:
Discharge Pressure: Monitoring pressure ensures stability in production processes.
Temperature Monitoring: Alerts for overheating help avoid lubrication degradation and equipment failure.
Energy Consumption: Tracking energy usage highlights inefficiencies and areas for improvement.
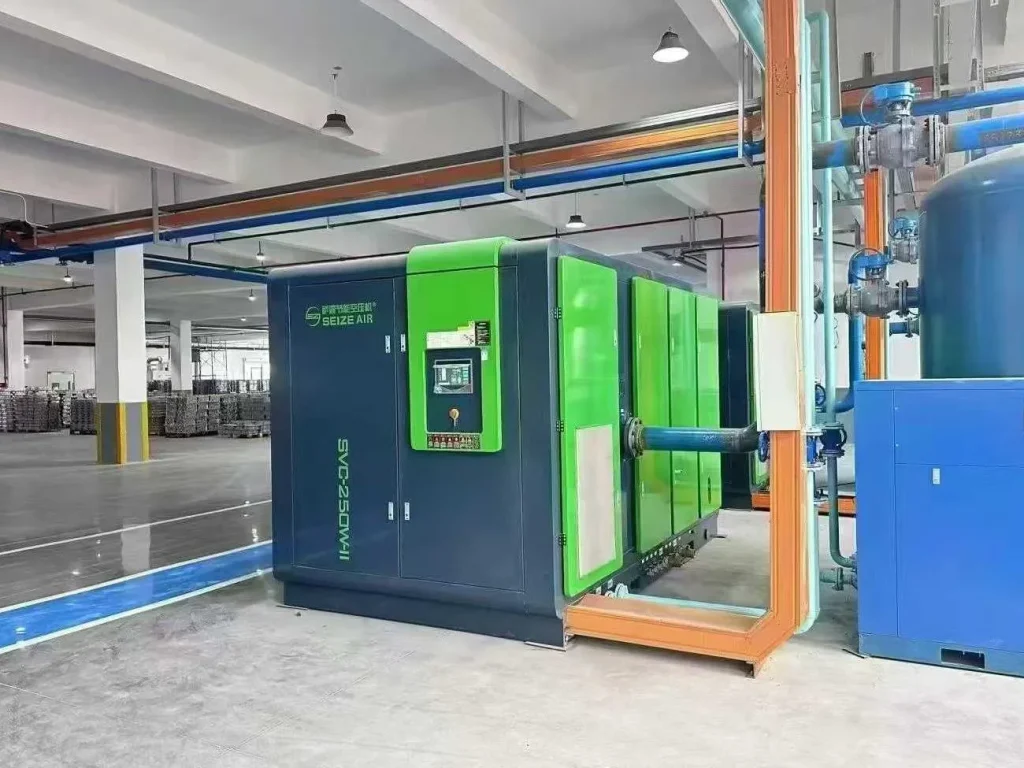
3. Fault Prevention: Reducing Downtime and Maintenance Costs
Proactively addressing common compressor faults can reduce repair costs and avoid disruptions:
Pressure Fluctuations: Caused by clogged filters or malfunctioning valves, regular checks can prevent this issue.
Overheating: Can lead to reduced oil quality and machine damage. Routine checks help maintain optimal temperature levels.
Abnormal Noise: Often indicates mechanical issues. Timely repairs prevent further damage.
4. Energy Optimization: Lowering Consumption and Boosting Efficiency
Energy costs are a significant part of compressor operation, and optimizing energy use is critical:
Variable Frequency Drive (VFD): VFDs adjust compressor speed based on demand, reducing energy consumption during low-load operations.
Heat Recovery: Reuse waste heat for other processes, lowering overall energy use.
Optimized Piping: Streamlining air pipes reduces friction, enhancing compressor efficiency.
Conclusion
Effective air compressor management involves regular maintenance, real-time monitoring, fault prevention, and energy optimization. By applying these strategies, businesses can improve efficiency, reduce costs, and extend the lifespan of their equipment, ultimately increasing their competitiveness. Investing in proper management and modern technologies is essential for maintaining reliable and cost-effective operations.