Introduction to Oil-Injected Screw Compressors
Oil-injected screw compressors are a cornerstone of modern industrial operations, powering everything from manufacturing plants to automotive workshops. Unlike oil-free or reciprocating compressors, these systems use oil to seal, cool, and lubricate internal components during the compression process. This unique design delivers unparalleled efficiency, reliability, and cost savings. In this article, we’ll explore the key benefits of oil-injected screw compressors and why they remain a top choice for industries worldwide.
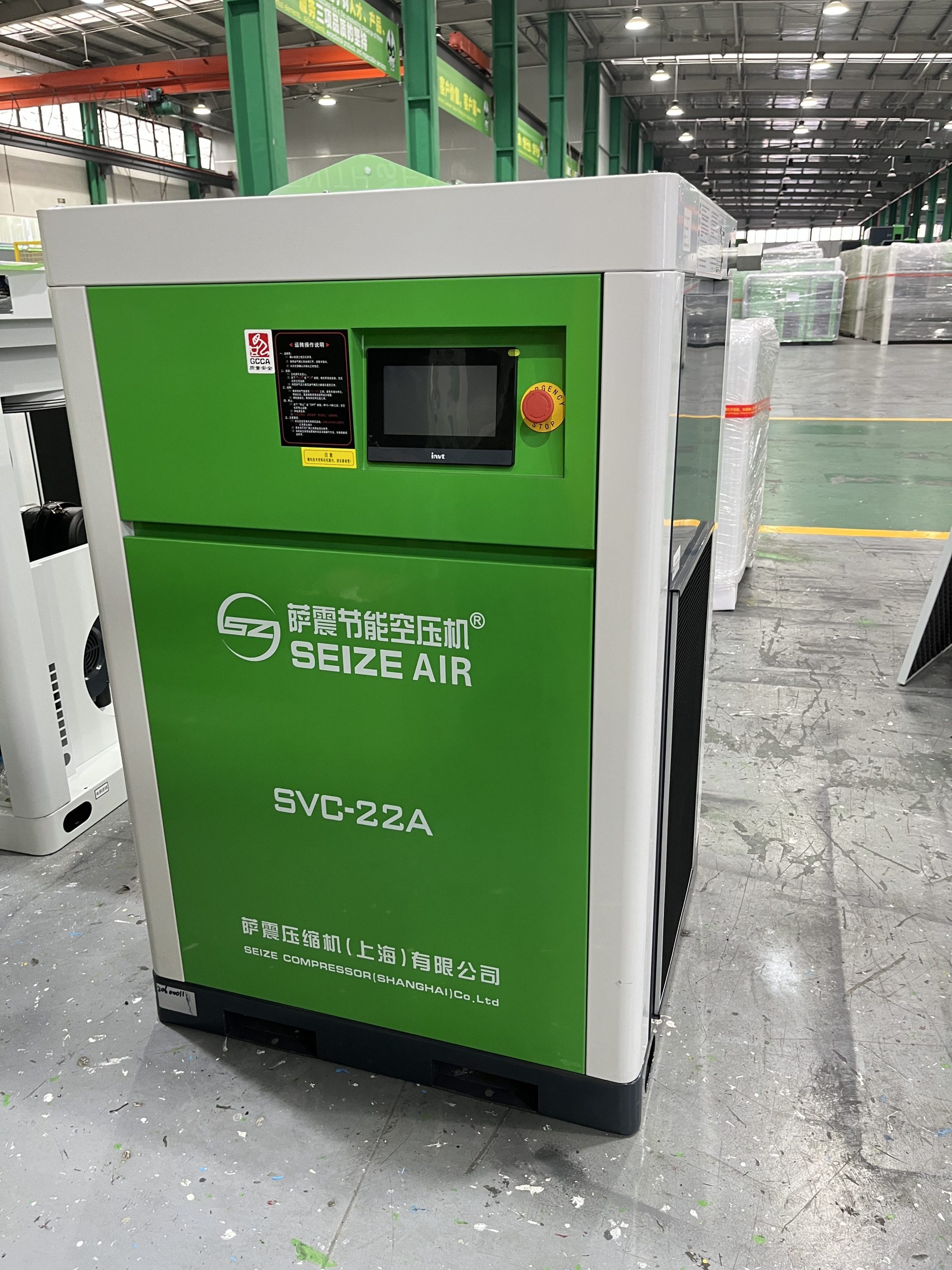
1. Superior Energy Efficiency
Reduced Power Consumption
Oil-injected screw compressors are engineered for optimal energy efficiency. The oil in the compression chamber acts as a coolant, reducing heat generation and minimizing energy loss. Studies show that these compressors consume 15–20% less energy compared to oil-free rotary screw models, translating to lower electricity bills.
Variable Speed Drive (VSD) Compatibility
Modern oil-injected compressors often integrate with variable speed drives (VSDs). VSD technology adjusts motor speed to match air demand, eliminating energy waste during low-load periods. For facilities with fluctuating air needs, this can reduce energy costs by up to 35%.
Case Study: Energy Savings in Automotive Manufacturing
A 2023 analysis of a German automotive plant revealed that replacing aging reciprocating compressors with oil-injected screw models cut annual energy costs by $120,000, with a payback period of under two years.
2. Exceptional Durability and Longevity
Robust Construction
Oil-injected screw compressors are built with heavy-duty components, including high-grade steel rotors and corrosion-resistant casings. The oil lubrication reduces wear on moving parts, extending the compressor’s lifespan to 60,000–80,000 hours before requiring major overhauls.
Reduced Thermal Stress
The oil’s cooling properties prevent overheating, a common cause of failure in oil-free compressors. This thermal stability ensures consistent performance even in 24/7 operations.
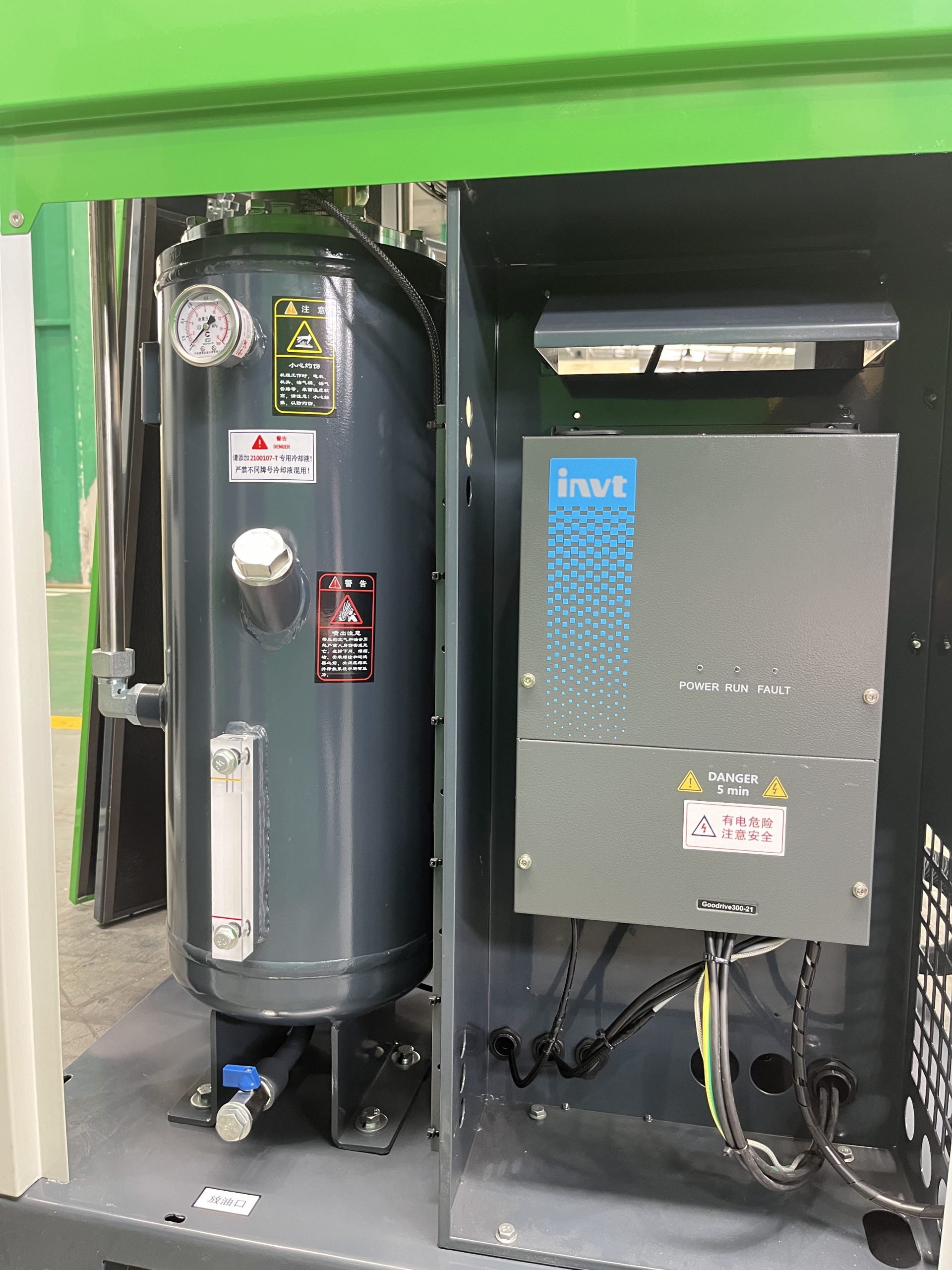
3. Lower Maintenance Costs
Simplified Maintenance Schedule
Oil-injected compressors require only basic routine maintenance, such as oil and filter changes. Unlike oil-free models, there’s no need for costly air treatment systems to remove moisture or contaminants.
Reduced Downtime
With fewer components prone to failure (e.g., no complex sealing systems), these compressors experience 40% less unplanned downtime than reciprocating or centrifugal alternatives.
Maintenance Checklist for Oil-Injected Screw Compressors
- Monthly: Inspect oil levels and air filters
- Quarterly: Replace oil filters and check for leaks
- Annually: Rotor alignment and motor inspection
4. Quiet Operation
Noise Reduction Technology
The oil layer dampens sound during compression, resulting in noise levels as low as 62–68 dB(A)—comparable to a normal conversation. This makes them ideal for indoor facilities where noise pollution is a concern.
Comparison with Oil-Free Compressors
Oil-free screw compressors operate at 75–85 dB(A), often requiring soundproof enclosures. Oil-injected models eliminate this added expense.
5. High-Quality Compressed Air Output
Minimal Contaminant Risk
While oil-free compressors are marketed as “contaminant-free,” they often require downstream filters to meet ISO 8573 air purity standards. Oil-injected compressors, when paired with proper filtration, deliver Class 0 oil-free air (less than 0.01 mg/m³ oil carryover).
Stable Pressure and Flow
The twin-screw design ensures pulsation-free airflow, critical for sensitive equipment like CNC machines or paint sprayers.
6. Versatility Across Industries
Applications of Oil-Injected Screw Compressors
- Manufacturing: Pneumatic tools, assembly lines
- Construction: Sandblasting, drilling
- Food & Beverage: Packaging, bottling (with food-grade oil)
- Pharmaceuticals: Tablet pressing, cleanroom processes
Case Study: Oil-Injected Compressors in Textile Manufacturing
A textile factory in India reported a 30% increase in productivity after switching to oil-injected screw compressors, thanks to stable airflow for automated looms.
7. Cost-Effective Initial Investment
Lower Upfront Costs vs. Oil-Free Models
Oil-injected screw compressors are 20–30% cheaper to purchase than oil-free equivalents. For small to mid-sized businesses, this makes them a budget-friendly choice.
Total Cost of Ownership (TCO) Analysis
While oil-free compressors have higher upfront costs, oil-injected models often deliver better TCO due to lower energy and maintenance expenses over a 10-year lifecycle.
8. Environmental Sustainability
Reduced Carbon Footprint
Energy-efficient operation cuts CO₂ emissions. For example, a 100 kW oil-injected compressor can save 45 tons of CO₂ annually versus older piston models.
Oil Recycling Programs
Many manufacturers offer oil recycling services, ensuring used lubricants are reprocessed rather than landfilled.
9. Adaptability to Harsh Conditions
Performance in Extreme Environments
Oil-injected compressors operate reliably in:
- High humidity (up to 95% RH)
- Dusty or abrasive atmospheres
- Temperatures from -10°C to 45°C
Case Study: Mining Operations in Australia
A mining company reported zero breakdowns in 18 months after deploying oil-injected compressors in its dusty, high-heat extraction sites.
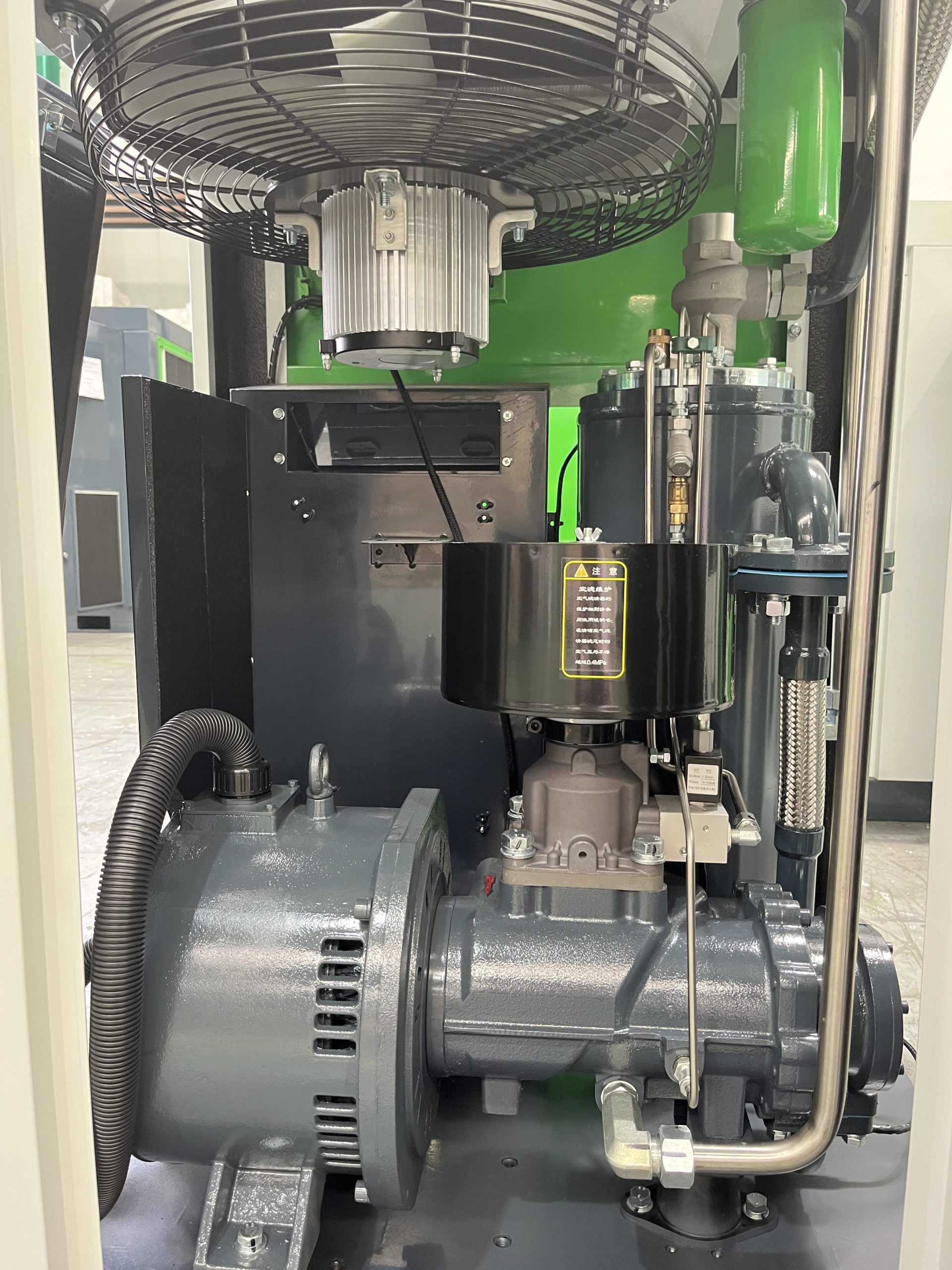
10. Future-Proof Technology
Integration with Industry 4.0
Modern oil-injected compressors feature IoT-enabled sensors for predictive maintenance and real-time performance monitoring via cloud platforms.
Compatibility with Renewable Energy
These compressors pair seamlessly with solar or wind power systems, supporting green manufacturing initiatives.
Conclusion: Why Choose Oil-Injected Screw Compressors?
From energy savings to rugged reliability, oil-injected screw compressors deliver unmatched value for industries seeking cost-effective, high-performance air compression. By prioritizing efficiency and ease of maintenance, they outperform oil-free and reciprocating alternatives in most real-world scenarios.
Pro Tip for Buyers: Always consult with a certified provider to match the compressor’s capacity (e.g., CFM, PSI) to your operational needs.
ℹ️Website: www.szaircompressor.com
☎️WhatsApp:https://wa.me/8615001719145
📧email:info@seize-air.com