Air Compressor Selection Guide
Selecting the right air compressor is essential for efficiency and cost-effectiveness. Here’s a concise guide to help you make an informed decision.
1. Air Demand and Pressure Requirements
Start by calculating the air flow needed for your operations, typically measured in CFM (cubic feet per minute) or L/s (liters per second). Consider the tools and machines that will use the compressed air, and add extra capacity for future needs. Also, determine the required pressure (PSI or Bar), typically between 90-120 PSI for general applications.
2. Compressor Type
Choose the right type of compressor for your needs:
Piston Compressors (Reciprocating): Best for smaller, intermittent use. They are affordable but require more maintenance and are noisier.
Screw Compressors (Rotary Screw): Ideal for continuous operations in medium to large industries, offering energy efficiency and lower maintenance.
Centrifugal Compressors: Suitable for large-scale industrial applications needing high volumes of air. They have high upfront costs but are efficient at higher flows.
Oil-Free Compressors: Used in industries requiring clean air, like food and pharmaceuticals. They cost more but avoid oil contamination.
3. Energy Efficiency
Choose energy-efficient models to reduce long-term operating costs. Look for compressors with features like variable speed drives (VSD) or variable frequency drives (VFD), which adjust output according to air demand. Energy certifications, such as ENERGY STAR, ensure compliance with high efficiency standards.
4. Maintenance and Durability
Consider the maintenance needs of the compressor. Piston compressors need more frequent upkeep, while screw and centrifugal models are generally more durable and require less maintenance. Assess the availability of spare parts and service options.
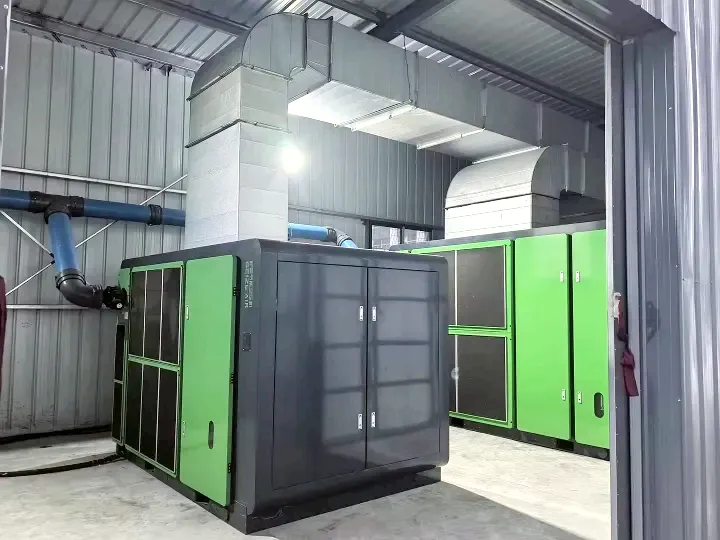
5. Installation and Space
Ensure there is adequate space for the compressor with proper ventilation, especially for cooling. Consider noise levels and accessibility for maintenance. Compressors may require a soundproof enclosure in noise-sensitive environments.
6. Operating Environment
Account for environmental factors like temperature, humidity, and dust. If operating in high temperatures or dusty conditions, select a model designed for such environments, possibly with built-in air filtration or drying systems.
7. Cost Considerations
While the initial cost is important, also consider operating costs (energy consumption) and maintenance expenses. More efficient compressors may have higher upfront costs but offer long-term savings.
8. Safety and Reliability
Ensure the compressor has safety features like overload protection, automatic shutoff, and pressure relief valves. Choose a reliable brand known for quality and service.
By considering these factors, you can select an air compressor that best meets your needs, improving productivity and reducing costs over time.