Air Compressor Management: Key Measures for Improving Production Efficiency and Energy Savings
Air compressors play a crucial role in industrial production. Proper management of air compressors not only helps reduce energy consumption but also enhances equipment operation efficiency. This article will introduce the core points of air compressor management, daily control measures, how intelligent management can improve energy-saving effects, and the importance of energy-saving culture and employee training.
1. Core Points of Air Compressor Management
The key factors in air compressor management include equipment selection, energy-saving control, maintenance, and optimization of operations. By making informed choices and optimizing various stages, energy consumption can be reduced, and the lifespan of equipment can be extended.
Equipment Selection and Energy-Saving Control
The selection of the right type of air compressor is vital for energy saving. Screw-type, piston-type, and centrifugal air compressors each have their distinct characteristics and are suited to different production needs. For optimal energy efficiency, it is recommended to use permanent magnet variable frequency air compressors, which adjust motor speed based on actual demand, avoiding energy waste.
Energy-Saving Technology Applications
In addition to efficient air compressor equipment, energy-saving technologies include pipe design, air storage tank configuration, and leak detection. Proper pipe design and system optimization can reduce airflow resistance, thereby lowering energy consumption.
2. Daily Control Measures in Air Compressor Management
Daily control measures include setting appropriate working pressure, performing regular maintenance, detecting air leaks, and optimizing startup/shutdown strategies. These measures help improve the operational efficiency of air compressors.
Setting Appropriate Working Pressure
The working pressure of the air compressor should be set according to actual needs. Excessive pressure not only wastes energy but also accelerates equipment wear. By using pressure sensors and automated control systems, working pressure can be adjusted precisely.
Regular Maintenance and Repair
Regular maintenance is critical for extending the lifespan of air compressors. Cleaning air filters, changing lubricating oil, and conducting comprehensive inspections help reduce mechanical wear and keep equipment running efficiently.
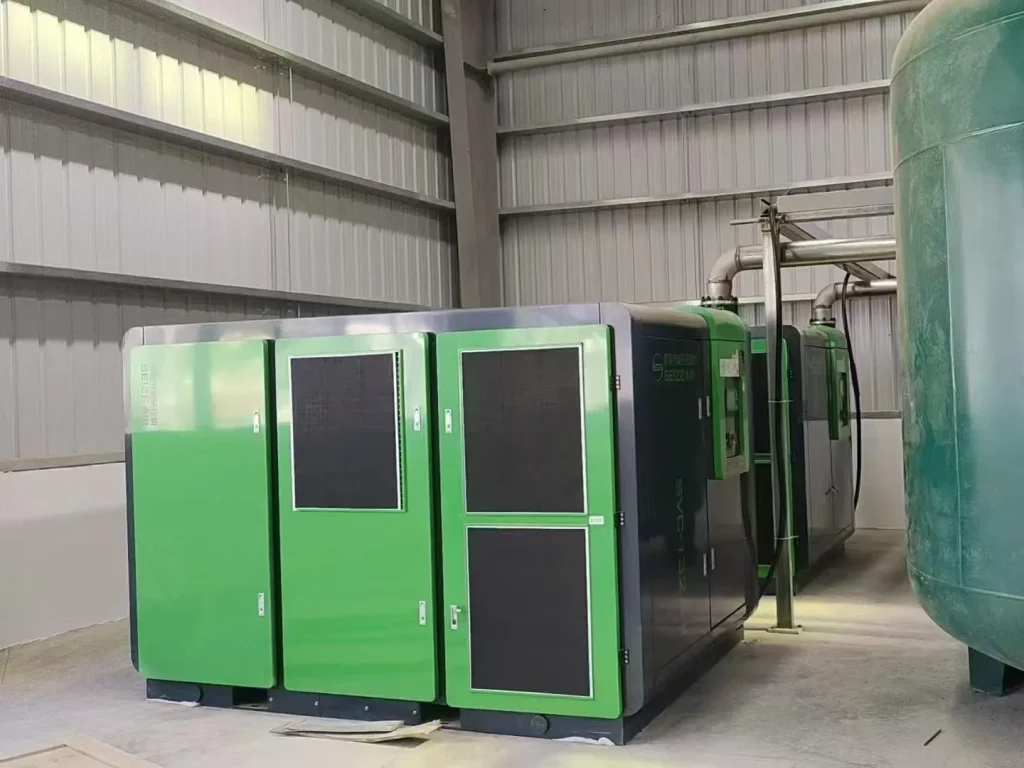
3. Intelligent Air Compressor Management for Enhanced Energy Savings
Intelligent management systems can monitor air compressor operations in real-time and automatically adjust operational parameters to further improve efficiency.
Intelligent Control Systems
Intelligent control systems use sensors and remote control technologies to collect and analyze real-time data from equipment. The system can adjust the air compressor’s operation mode based on actual gas demand, optimizing load and reducing energy consumption.
Data Analysis and Energy Consumption Optimization
By analyzing the operating data of air compressors, companies can identify energy-saving opportunities. For example, intelligent systems can adjust operational modes based on load fluctuations, reducing frequent startups and shutdowns, which minimizes energy waste.
4. Energy-Saving Culture and Employee Training
In addition to equipment and technological optimization, establishing an energy-saving culture and improving employee awareness of energy-saving practices are also crucial. Regular energy-saving training helps enhance employees’ operational efficiency and reduces energy wastage.
Establishing an Energy-Saving Management System
Companies should develop energy-saving operational guidelines and establish energy-saving responsibility systems. Clearly defined energy-saving tasks for each role and incentive mechanisms can encourage employees to actively participate in energy-saving efforts.
Enhancing Employee Energy-Saving Awareness
Regular training sessions on energy-saving awareness help reduce human errors that lead to energy waste. Fostering a sense of responsibility among employees ensures that equipment operates efficiently at all times.
Conclusion
Air compressor management is a systemic process that includes equipment selection, technological improvements, daily maintenance, and intelligent control. Proper management can significantly reduce energy consumption, increase production efficiency, and drive sustainable development. With the continuous advancement of intelligent technologies, future air compressor management will become more refined and intelligent, generating greater benefits for industrial production.