Compressed air quality standards: ensuring industry safety and efficiency
Compressed air quality standards are critical in modern industrial and commercial applications, ensuring that compressed air can meet the requirements of safety, reliability and efficiency in various applications. Whether it is manufacturing, pharmaceuticals, food processing or electronics, proper compressed air quality directly affects the smooth progress of the production process.
Compressed air quality standards vary depending on the application field, but generally involve the following aspects:
Cleanliness requirements: Compressed air must be free of contaminants such as impurities, moisture, and oil. Contaminants can cause equipment damage, affect product quality, and may cause production interruptions. In many industries, cleanliness is the basic standard for ensuring compressed air quality.
Dryness control: The moisture content in compressed air directly affects the operation of equipment and the quality of products. Excessive moisture may cause equipment corrosion or affect the stability of the production process. According to different industry requirements, dryness standards usually require that the dew point temperature of compressed air must be kept within a certain range to prevent moisture condensation.
Oil content requirements: Oil control in compressed air is particularly important, especially in industries such as pharmaceuticals and food processing that have extremely high requirements for air quality. For example, according to the Chinese Pharmacopoeia and GMP (Good Manufacturing Practice), the oil content in compressed air must be strictly controlled, usually not exceeding 0.1mg/m³.
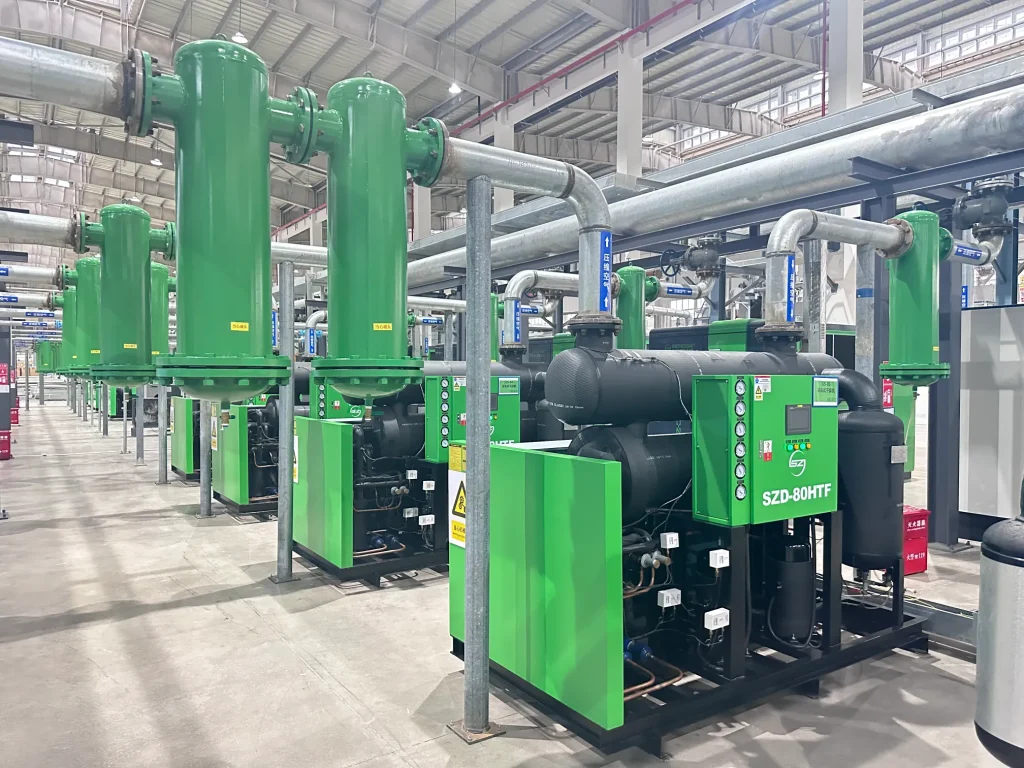
Microbial and particle control: In the pharmaceutical, medical and food processing fields, pollutants such as microorganisms, particles, grease, etc. in compressed air must be strictly controlled. These pollutants may have adverse effects on product safety and quality, so the compressed air used in these fields needs to meet the sterility requirements, and the particle size should be less than or equal to 0.1μm.
Pressure dew point requirements: The pressure dew point of compressed air (i.e. the condensation temperature of water vapor) must be lower than the specified temperature to prevent moisture from condensing into liquid inside the equipment, thereby preventing equipment corrosion and product moisture. Dew point control is an important parameter to ensure the quality of compressed air.
Dust particle size standard: Different industries have different requirements for dust particle size in compressed air. Generally speaking, solid particles in compressed air must meet specific particle size requirements, such as less than 0.1μm, to ensure that they meet cleanliness standards.
Sterility requirements: Especially in drug packaging and direct drug contact applications, compressed air must be sterilized to ensure that it meets sterility standards. This is an important guarantee to ensure product quality and consumer safety.
Odor control: The smell of compressed air should be neutral and free of odor. The presence of odor may have an adverse effect on the production environment and product quality, especially in industries with extremely high requirements for air purity.
Compressed air quality standards are an indispensable part of modern industrial production. It not only ensures the normal operation of equipment, but also plays a vital role in production efficiency and product quality. By optimizing compressed air quality management, enterprises can achieve efficient, safe and pollution-free production processes and promote the healthy development of various industries.
《“Compressed air quality standards: ensuring industry safety and efficiency”》 有 1 条评论
hhh