The waste-to-energy (WtE) industry is rapidly evolving as cities worldwide seek sustainable solutions to manage growing volumes of municipal solid waste (MSW) while generating clean electricity. At the heart of this process lies a critical yet often overlooked component: air compressors. As a leading innovator in air compressor technology, Seize Air showcased its cutting-edge solutions at the 2025 Waste Incineration Power Generation Conference & Forum in Changsha, emphasizing how its energy-efficient systems empower the sector’s green transformation.
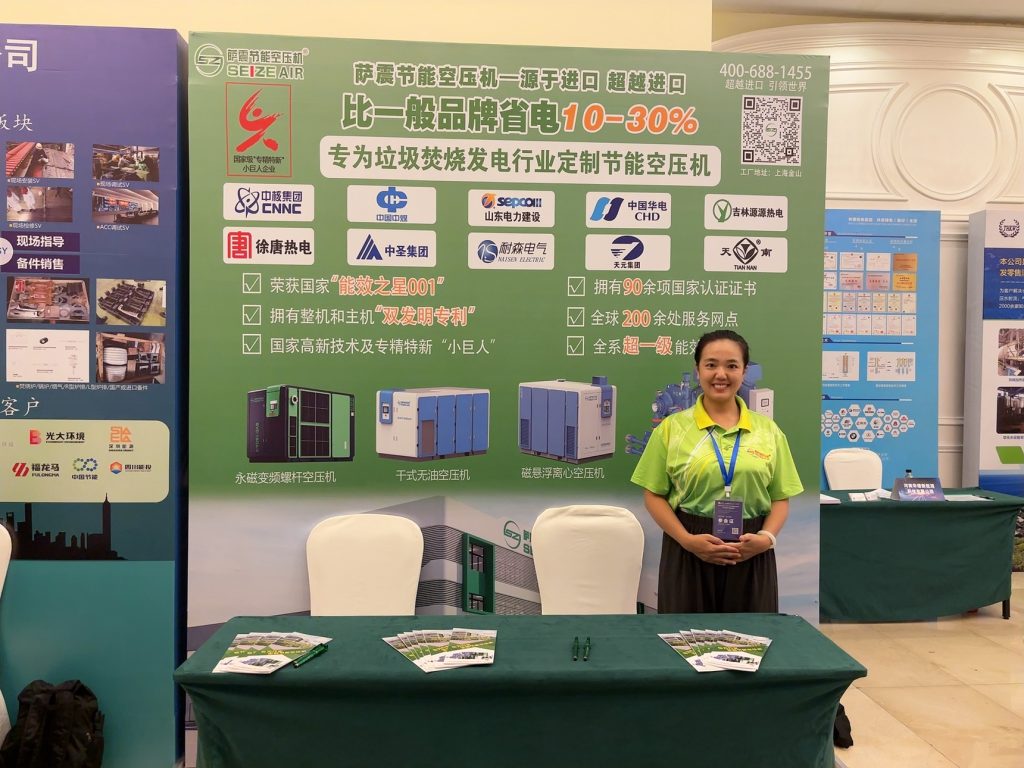
The Role of Air Compressors in Waste-to-Energy Plants
In garbage incineration power plants, air compressors are indispensable across multiple stages:
- Combustion Air Supply: Precise airflow control ensures optimal incineration temperatures, maximizing energy output and minimizing harmful emissions.
- Automation & Instrumentation: Compressed air powers pneumatic valves, actuators, and control systems critical for safe, efficient plant operations.
- Flue Gas Treatment: Air compressors support scrubbers and bag filters to neutralize pollutants like SOx, NOx, and particulate matter.
- Material Handling: From waste sorting to ash removal, compressed air drives conveyor systems and pneumatic tools.
Without reliable, high-performance air compressors, WtE plants risk operational downtime, reduced energy recovery, and non-compliance with environmental regulations.
SeizeAir: Pioneering Energy Efficiency in the WtE Sector
As a Top-Tier Chinese Air Compressor Manufacturer, SeizeAir has cemented its reputation by delivering tailored solutions for the waste-to-energy industry. At the Changsha forum, SeizeAir engineers highlighted three core advantages that set its systems apart:
1. Unmatched Energy Savings
WtE plants operate 24/7, making energy consumption a major cost driver. SeizeAir’s variable frequency drive (VFD) compressors reduce power usage by up to 35% compared to fixed-speed models. Intelligent pressure modulation ensures airflow precisely matches demand, eliminating wasteful “load/unload” cycles.
2. Industry-Leading Reliability
SeizeAir compressors integrate AI-powered predictive maintenance and corrosion-resistant components engineered to withstand harsh environments (high temperatures, dust, and corrosive gases). This minimizes downtime, a critical factor for WtE plants where interruptions cost thousands per hour.
3. Sustainability Alignment
By slashing energy use and carbon footprints, SeizeAir supports WtE facilities in achieving dual-carbon goals. For example, a 100-ton/day plant using SeizeAir compressors can cut CO2 emissions by 120+ tons annually—equivalent to planting 5,500 trees.
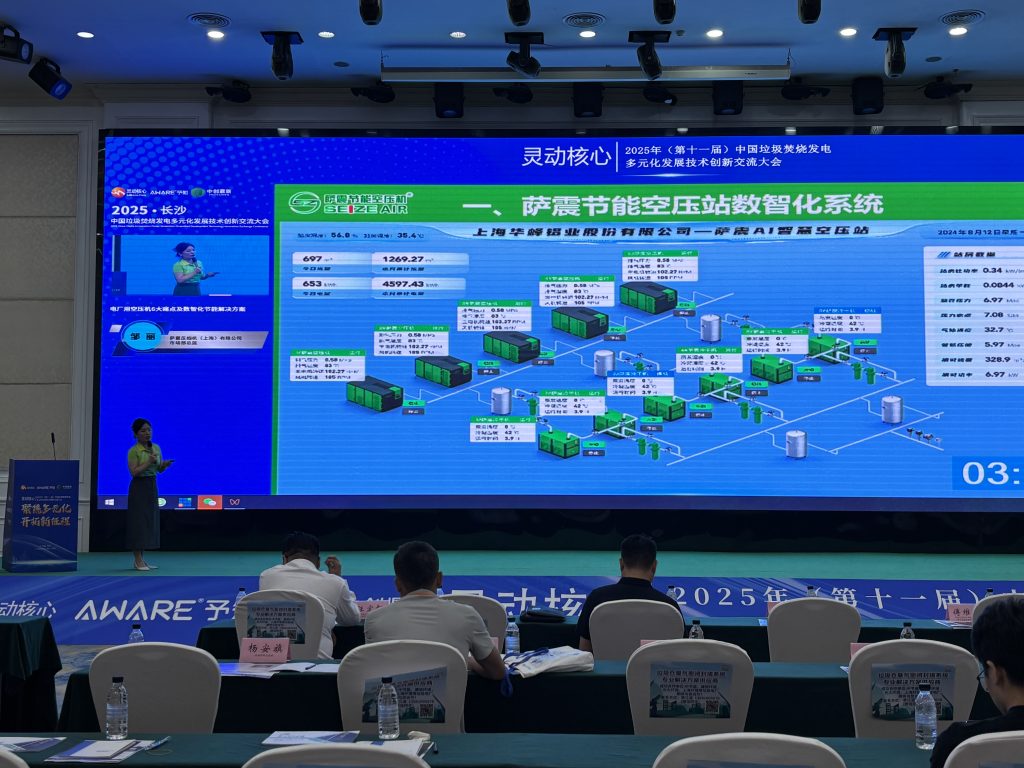
Case Study: SeizeAir in Action
A Jiangsu-based WtE plant upgraded to SeizeAir’s GA-75+ VSD screw compressor in 2024, achieving:
- 30% lower energy costs ($18,000 saved annually)
- 40% reduction in maintenance expenses via smart diagnostics
- Compliance with China’s GB 19153-2019 efficiency standards
Why Choose SeizeAir for Your WtE Project?
- 25+ Years of Expertise: Deep understanding of WtE workflows and challenges.
- Customized Solutions: Compressors optimized for flue gas treatment, combustion control, and more.
- Global Certifications: ISO 8573-1 Class 0 oil-free air options for sensitive applications.
Conclusion
The waste-to-energy sector’s success hinges on efficient, dependable compressed air systems. By prioritizing innovation and sustainability, SeizeAir has emerged as a trusted partner for WtE plants worldwide. As demonstrated at the Changsha conference, its energy-saving compressors not only reduce operational costs but also align with global carbon neutrality initiatives.
Ready to optimize your WtE plant’s performance? Contact SeizeAir today to explore how our advanced air compression solutions can power your green energy goals.
Internal Links:
发表回复