Preventive Measures for Screw Air Compressor Not Loading
Screw air compressors are widely used in industrial production, and their stability directly affects production efficiency. A failure to load is a common issue that can lead to downtime and equipment damage. Below are some effective preventive measures to avoid this problem.
1.Regular Maintenance
Regular maintenance is key to preventing the air compressor from failing to load. Keeping the equipment clean and lubricated, and regularly checking and replacing consumable parts such as air filters, oil separators, and lubricating oil, ensures that the compressor operates at its best. Regular oil changes are especially important, as they reduce friction and wear, extending the service life of the machine.
Key Points:
Regularly clean the air filters and cooling system.
Periodically change the lubricating oil and filters.
Clean the intake pipes to maintain smooth airflow.
2.Check the Electrical Control System
The electrical control system of a screw compressor is responsible for controlling its start-up and shutdown. Any electrical failure can prevent the compressor from loading. Regularly check electrical components such as wiring, sensors, and control panels to ensure they are functioning properly, and replace any damaged parts in a timely manner.
Key Points:
Check if electrical components are loose, aged, or damaged.
Ensure that sensors and the control system are operating normally.
Regularly check the cables for wear or damage.
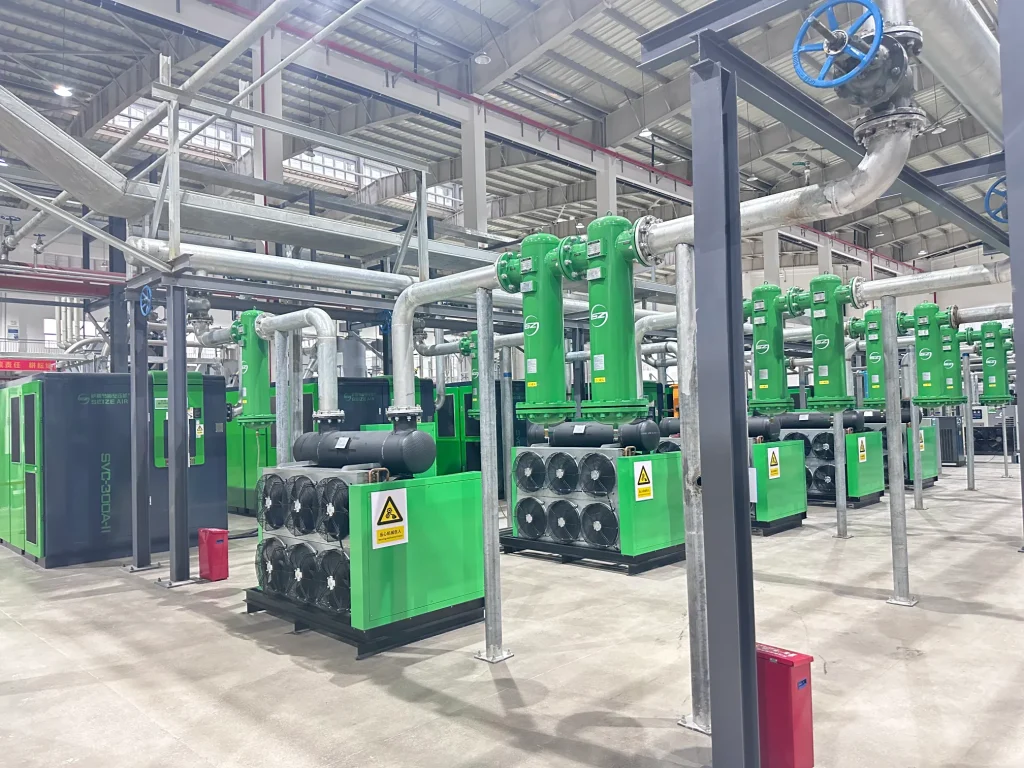
3.Inspect the Piping System
The piping system of the compressor is responsible for the transportation and distribution of air. Leaks or blockages in the pipes can affect the compressor’s loading. Regularly check the tightness of the piping and repair any leaks promptly. Additionally, clean the pipes to remove impurities such as moisture and oil, which could affect the compressor’s operation.
Key Points:
Inspect the pipe joints and the pipes themselves for leaks.
Periodically clean the pipes to avoid water and oil buildup.
Ensure that airflow in the pipes is unobstructed.
4.Follow Operating Procedures
Proper operating procedures are crucial to preventing the compressor from failing to load. Operators should adhere to standard start-up and shut-down procedures and avoid prolonged overload operation. Continuous overloading increases the load on the equipment, affects its performance, and may even prevent the compressor from loading.
Key Points:
Operate the compressor according to standard start-up and shut-down procedures.
Avoid prolonged overload operation.
Regularly monitor parameters such as pressure and temperature.
A screw air compressor failing to load is usually caused by equipment aging, improper operation, or system malfunctions. Through regular maintenance, checking the electrical and piping systems, and adhering to proper operating procedures, the likelihood of failures can be significantly reduced, and the service life of the equipment can be extended. Companies should prioritize the management and maintenance of air compressors to ensure stable, long-term operation, thereby ensuring the efficient operation of production lines.