Emergency Response Procedure for Air Compressor Failures
Air compressors are crucial pieces of equipment in various industrial sectors, playing a key role in ensuring efficient production and maintaining product quality. However, due to factors like equipment wear, operational errors, or environmental influences, air compressors may experience failures from time to time.
1.Failure Detection and Initial Response
Failure Identification: When an air compressor experiences a malfunction, operators should immediately stop the machine and cut off the power supply to prevent further damage. Observing failure symptoms such as abnormal noises, vibrations, temperature fluctuations, and checking indicator readings like pressure, temperature, and current can help in diagnosing the issue.
On-Site Evaluation: Once the emergency response team arrives on-site, a comprehensive assessment of the failed equipment should be conducted. This includes identifying the type and severity of the failure, assessing its impact on production, and evaluating potential risks. Based on this evaluation, a specific action plan will be developed.
Safety Measures: Before handling the failure, necessary safety precautions must be taken. This includes wearing appropriate personal protective equipment (PPE), setting up safety barriers to restrict access to the area, and ensuring proper ventilation to avoid exposure to harmful gases or dust.
2.Steps for Troubleshooting and Repair
Power Supply Check: The first step in troubleshooting an air compressor failure is to check the power supply. If there’s an electrical fault, immediate repairs or replacement should be performed. Also, ensure that the electrical system is free from issues like short circuits or open circuits.
Control Circuit Inspection: Next, check the control circuit of the air compressor. In case of any faults such as blown fuses or damaged contactors, replace the faulty components and investigate the root cause of the malfunction.
Lubrication and Cooling System Check: Inspect the lubrication and cooling systems to ensure they are functioning correctly. If the lubrication is insufficient or the cooling system isn’t working as expected, the machine should be stopped for an inspection, and any necessary parts should be replaced or cleaned.
Mechanical Component Inspection: Mechanical components, such as bearings, gears, and belts, should be checked for wear or damage. If any parts are found faulty, they should be replaced or repaired immediately to restore the compressor’s efficiency.
Sensor and Instrumentation Check: Verify that all sensors and instruments, such as pressure gauges, temperature sensors, and flow meters, are functioning properly. Any malfunctioning sensors or instruments should be repaired or replaced to ensure accurate monitoring and control.
Address Other Faults: If the previous steps do not resolve the issue, additional components like the compressor head, intake valve, or exhaust valve should be inspected. Based on the observed symptoms and results of these checks, further troubleshooting and corrective actions will be carried out.
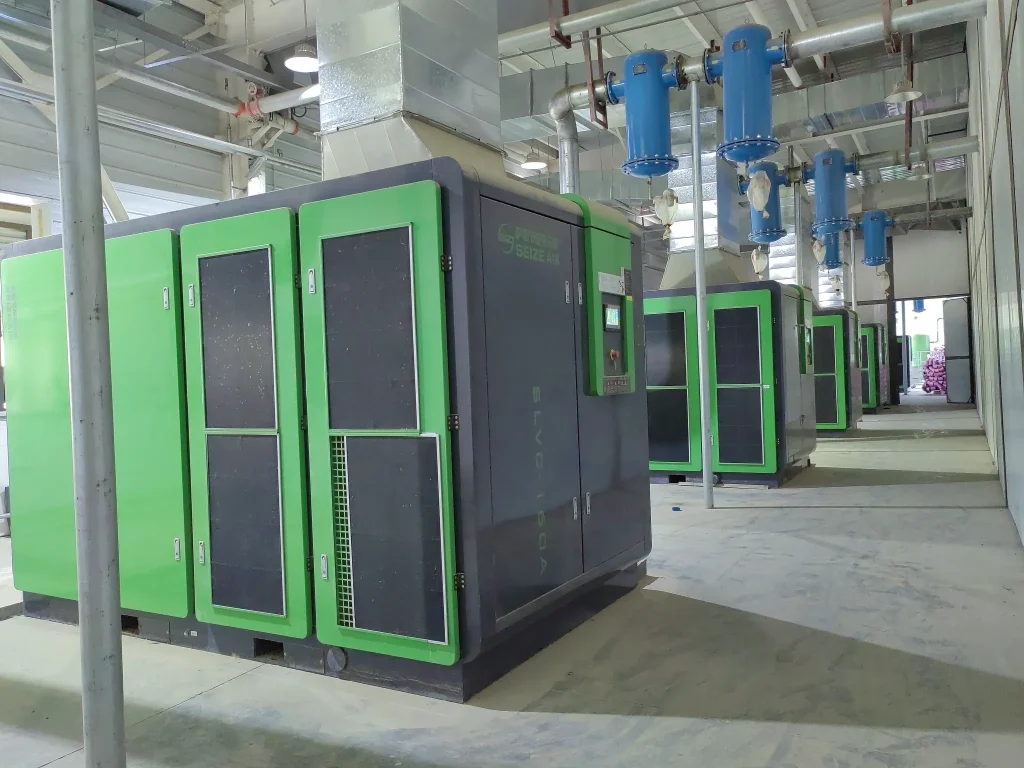
3.Post-Failure Analysis and Improvement
Failure Analysis: Once the failure has been resolved, a detailed analysis should be conducted. This analysis should focus on the root cause of the failure, the repair process, and the effectiveness of the measures taken. This evaluation helps in understanding potential hidden risks and provides valuable insights for future preventive actions.
Improvement Measures: Based on the findings of the failure analysis, corrective and preventive measures should be developed. These measures could include optimizing equipment design, strengthening regular maintenance procedures, and enhancing the technical skills of operators. These improvements should be incorporated into the equipment management and operational guidelines to ensure long-term stability.
Training and Education: In light of the issues identified during the failure response process, relevant personnel should undergo additional training and education. This will help improve their understanding of air compressor systems and enhance their ability to troubleshoot and resolve future failures efficiently.
Plan Revision: The emergency response plan should be revised and improved based on the practical experience gained during the failure resolution process. This revision should ensure that the plan is scientifically sound, practical, and easy to implement, thus providing stronger support for future emergency responses.
By implementing a rigorous emergency response procedure and effective improvement measures, companies can ensure that air compressor failures are addressed quickly and efficiently, minimizing downtime and maintaining production safety and product quality. Regular maintenance, enhanced operator training, and continuous evaluation of the emergency response plan are critical in preventing unexpected failures and ensuring the long-term reliability of air compressors.