Energy-Saving Testing Measures for Air Compressors
Air compressors are crucial equipment in industrial production, consuming a large amount of energy. Energy-saving testing of air compressors involves analyzing operational data to help companies reduce electricity consumption, lower carbon emissions, and improve efficiency. This leads to reduced production costs and enhances environmental sustainability.
Methods and Requirements for Energy-Saving Testing of Air Compressors
Testing Conditions: Tests should be conducted when the air compressor unit and gas supply system are operating normally to ensure the results are representative. For compressors with stable loads, the testing period should be at least 2 hours. For compressors with unstable loads, tests should be conducted based on the load fluctuation cycle.
Sampling and Measurement: During the testing, each parameter should be sampled at least 3 times, with an interval of 10-20 minutes to ensure accuracy. The volume flow rate is measured using a flow meter, and the measurement instruments should comply with national standards and be within their validity period.
Testing Parameters:
Gas Flow Measurement: Accurate measurement using a thermal mass flow meter or ultrasonic flow meter.
Compressor Load Rate Detection: Real-time monitoring of compressor power consumption and load rate to assess energy-saving effectiveness.
Inlet Pressure Detection: Monitoring the inlet pressure using a pressure gauge to ensure it remains within a reasonable range to reduce energy consumption.
Exhaust Temperature Detection: Exhaust temperature reflects compressor load conditions, which can be measured using a thermocouple.
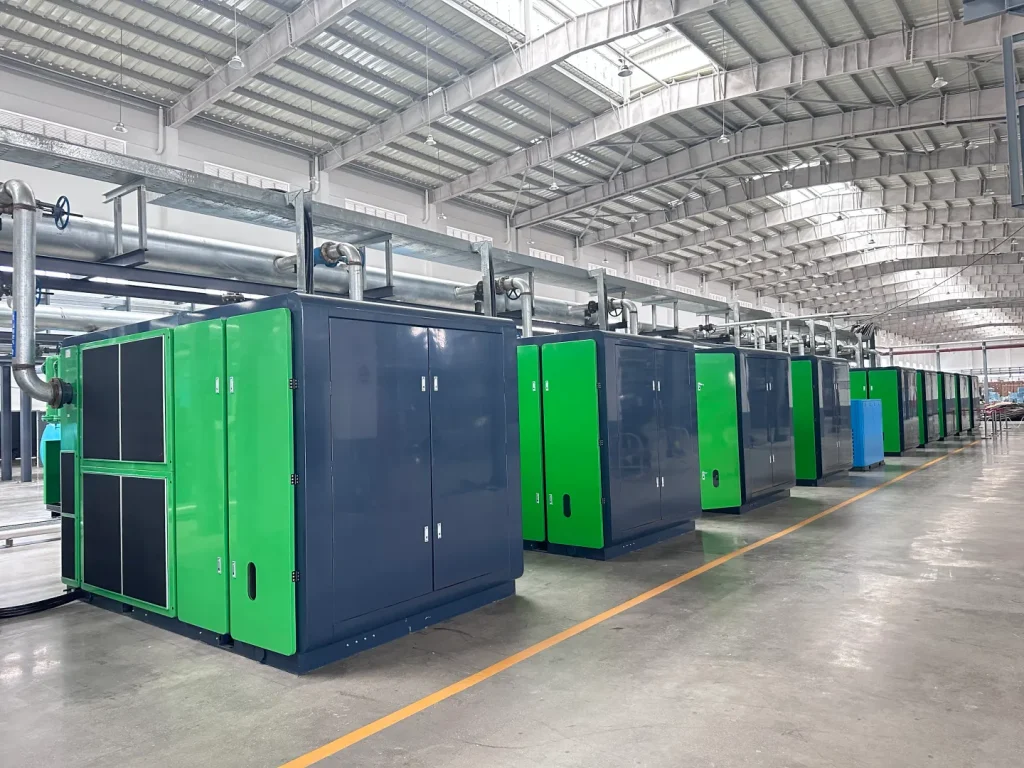
Steps for Implementing Energy-Saving Testing
Preparation Stage: Define testing goals and scope, prepare relevant testing equipment (e.g., flow meters, thermometers, pressure gauges), and develop a detailed testing plan.
Implementation Stage: Conduct on-site testing according to the plan, collect data for various parameters, and analyze the results. Compute statistical indicators and write a testing report.
Improvement Stage: Based on the test results, develop an energy-saving improvement plan, implement energy-saving measures (such as replacing with more efficient equipment, optimizing the gas supply system, enhancing maintenance), and conduct follow-up testing to verify the effectiveness of the improvements.
Energy-saving testing for air compressors helps companies reduce energy consumption, decrease emissions, and enhance environmental benefits. By precisely monitoring key parameters such as gas flow, load rate, pressure, and temperature, efficient energy-saving modification plans can be developed to improve the competitiveness of the company.